Recommended Stories
Nearmap’s AI-powered models approved in 27 markets
Insurers can leverage the predictive scores to help price risk.
WalletHub: States where auto loan rates increased the most
New car buyers are in a financial squeeze.
Shifting weather patterns challenge future flood prediction
New technology juggles storm water risk, urbanization and climate change.
Resource Center

eBook
Sponsored by AgentSync
The Future of P&C Insurance: The Race to Contain Costs Amid Rising Catastrophic Losses
The P&C insurance sector is currently facing challenges. This eBook outlines the most pressing problems, the most promising solutions, and a few examples of these principles in action.

Case Study
Sponsored by CoreLogic
Revolutionizing Claims Processing: How a Leading Insurer Transformed Water Mitigation Reviews
Discover how one insurer drastically improved the efficiency of their water mitigation claim reviews, reducing costs and time while enhancing decision-making. Learn how this approach can transform your claims process, making it faster, more accurate, and less resource-intensive.

Assessment
Sponsored by AgentSync
Distribution Channel Management Assessment
Navigating today’s insurance landscape requires more than instinct. Assess the strengths and gaps in your distribution strategy with this comprehensive tool. Discover actionable insights to refine operations, enhance data quality, ensure compliance, and scale efficiently. Evaluate your current capabilities and see where you stand across five crucial areas. Start building a more resilient and agile network today.
PropertyCasualty360
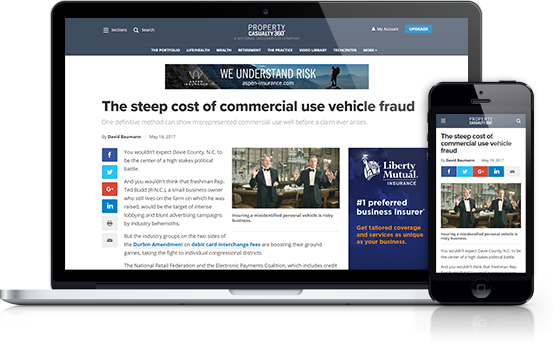
Don’t miss crucial news and insights you need to make informed decisions for your P&C insurance business. Join PropertyCasualty360.com now!
- Unlimited access to PropertyCasualty360.com - your roadmap to thriving in a disrupted environment
- Access to other award-winning ALM websites including BenefitsPRO.com, ThinkAdvisor.com and Law.com
- Exclusive discounts on PropertyCasualty360, National Underwriter, Claims and ALM events
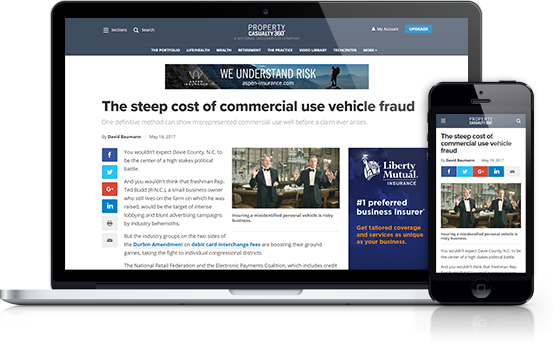
Copyright © 2024 ALM Global, LLC. All Rights Reserved.